Extrusion is by far the most complex and delicate phase of the long process of manufacturing aluminium alloy profiles. It requires a high degree of technology but also the technical skill and experience which only a large company like All.co, with its extensive equipment and long experience in the field, is able to exploit to the full.
The extrusion process starts with the creation of steel dies designed by expert technicians using the latest software for two- and three-dimensional design. Our highly equipped in-house technical workshop – which meets practically the entire needs of the Group – transforms the designs into physical models, using computerized systems which control the work centres, the lathes and the electro-discharge machines. Final checking of the dies is carried out by experienced and skilled operators, ensuring that the results are up to the required standard of execution.
The aluminium billets, heated to the appropriate temperature, are pushed under pressure through the dies and transformed – through the extrusion process – into long sections. We have seven presses with varying powers of from 1600 to 5000 tons. This gives All.co a high productive capacity and means it can provide both small-size extruded items and medium to large products, up to 14 metres in length and weighing up to 50 kg/ml (see here for a table showing product size limits). Extrusion is carried out in line with minimum working tolerances to ensure the perfect assembly of the components produced and to simplify the process of obtaining quality certification for the end products.
Following extrusion the profile stretchings are pressed, ensuring that they are perfectly straight and the precise geometrical shape required. They are then sent for cutting and finally for ageing, which may be done either naturally or in furnaces where the molecular structure of the metal is strengthened, providing the extruded products with better qualities of compactness and durability. The manufacturing process ends at the packing station, where the profiles are appropriately prepared to protect them during the subsequent phases of storage, transport or forwarding to the finish plant.
All.co offers its clients valuable and on-going assistance which aims at producing the best possible design, processing and execution times for the profiles and at providing a positive response to our clients’ various technical and aesthetic requirements. A tried and tested procedure allows tracking of client requests and monitoring of project state of progress.
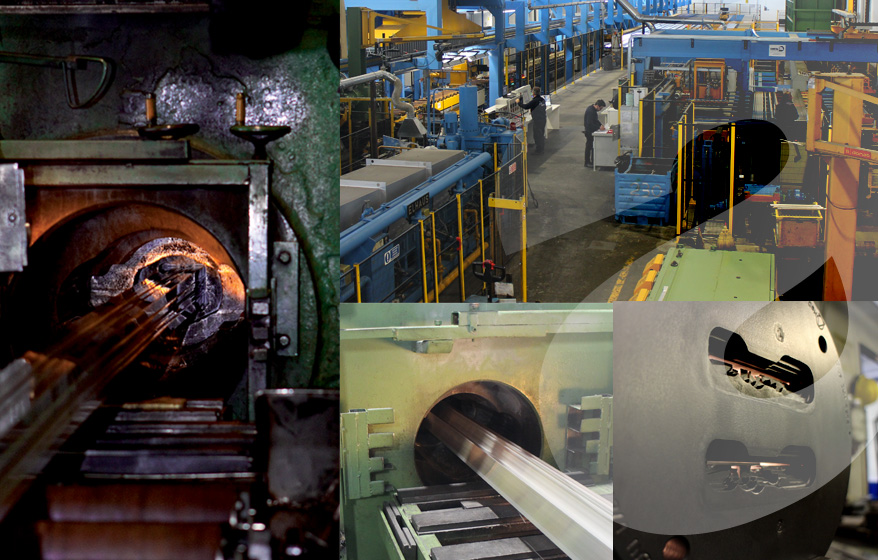